Die ersten vier Bautage sind um und das Fundament fürs Tiny House ist gelegt: Der sogenannte Subfloor ist seit gestern Abend fertig! :-)
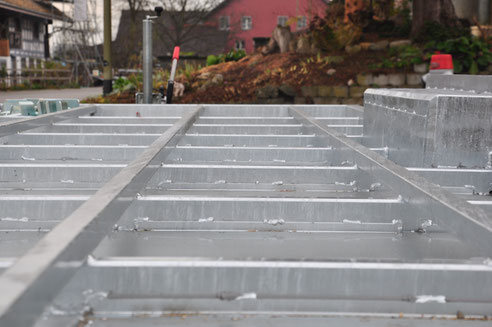
Ein Nachwort zum Tiny-House-Anhänger
Wer gleich zum Bautagebuch möchte, bitte runterscrollen - hier folgt zuerst noch ein abschliessendes Wort zur Anhängergeschichte. Im letzten Beitrag hab ich den Anhänger, den ich nun doch noch bekommen habe, ja ziemlich detailliert beschrieben. Und ausführlich über die Abnahme gebrabbelt. Diese Detailtreue werde ich, zwecks wichtiger Bau-Infos, nicht noch einmal an den Tag legen, aber es wäre schade, wenn das Ende der Anhänger-Warte-Ära nicht kommentiert würde:
Am Tag nach der Anhänger-Abnahme hatte ich noch einmal ein Telefongespräch mit Herrn Stüssi, das fast eine halbe Stunde lang ging. Ich gab ihm eine ausführliche Rückmeldung zum Anhänger, erläuterte zuerst alle positiven Aspekte, und ging dann zu den kritischen Punkten über (fehlendes Schloss, fehlende Teleskopkurbelstützen, fehlende Abschluss-Bleche, ein Blech zu viel drin, überflüssige Löcher im Chassis etc.). Wie war die Reaktion / Erklärung vom Anhängerprofi zu den einzelnen Punkten?
- Fehlendes Schloss: Wie versprochen wurde mir kurz danach ein Schloss an meine Adresse geschickt; es hängt jetzt bereits am Anhänger und schützt das zukünftige Tiny House davor, gestohlen zu werden.
- Fehlende Teleskopkurbelstützen: Statt der 4 St¨ützen, die hätten am Anhänger angeschweisst sein sollen, hatte ich 8 mobile Stützen bekommen, die man unter den Anhänger stellen kann. Die Erklärung, weshalb Stüssi keine Teleskopkurbelstützen befestigt hatte: Solche Teleskopkurbelstützen dürfen laut Gesetz nur je 150kg tragen; das Tiny House (~3500kg) wird zu schwer sein für die Stützen. Deshalb habe Stüssi mir die 8 flexiblen Stützen mitgegeben. Auf ihnen kann sich das Gewicht des Tiny House besser verteilen. Positiv überrascht hat mich das Angebot, dass Stüssi mir die Telekskopkurbelstützen in Zukunft trotzdem noch befestigen würde, wenn ich wollte.
- Die 12 Löcher: Stellt sich heraus, dass diese tatsächlich Löcher für Zurrhaken sind (normalerweise wird ja eine Ladung auf einem Anhänger festgezurrt, die Haken brauchen Löcher.) Der Werkstattleiter hatte diese Löcher fälschlicherweise am Schluss noch reingebohrt, weil er keine Löcher auf dem Bauplan sah (was ja beabsichtigt war) und dachte, das hätte man vergessen... Stüssi habe keine Zeit gehabt, mich darüber zu informieren; er habe sich geärgert, als er den Fehler bemerkt hatte.
- Das Loch beim Vorplatz, das mit Blech verschlossen war: Hatte Stüssi vergessen, hat sich aber am Telefon wieder daran erinnert.
- Die fehlenden Blechabschlüsse: Hatte Stüssi ebenfalls vergessen, sich aber am Telefon wieder erinnert. Ärgerlich, da es schriftlich festgehalten war...
- Gebogene Bleche statt Winkeleisen: Es ging tatsächlich darum, beim Anhänger Gewicht zu sparen. Deshalb hatten sie sich gemeinsam mit dem Statiker für ein sogenanntes "Z-Profil" und gegen ein angeschweisstes Winkeleisen entschieden. Der Statiker und Stüssi haben gewusst, dass die Wände an dieser Stelle stehen würden und der Statiker hat ausgerechnet, dass die geringere Dicke des Z-Profils im Vergleich zum Winkeleisen kein Problem für die Statik sein sollte. Das klingt alles gut und recht, trotzdem habe ich von Stüssi eine schriftliche Bestätigung des Statikers verlangt, in der steht, dass die Z-Profile halten sollen. Leider ist die noch nicht eingetroffen und bevor ich die nicht habe, werde ich den Anhänger nicht bezahlen.
- Zum Schluss haben wir über den Preisnachlass gesprochen, den ich nun tatsächlich mehr oder weniger in der Höhe bekomme, wie ich ihn mir vorgestellt hatte.
Fazit: Ich habe nun (fast) alles bekommen, was mir wichtig war (Erklärungen, Schloss, Stützen, Preisnachlass), aber eines lässt sich trotzdem nicht wegreden: Die Kommunikation zwischen der Firma Stüssi und mir als Kundin war mehr als einmal holprig. Die Erklärungen, die ich für die fehlenden/¨überflüssigen Teile am Anhänger bekommen habe, sind zwar einleuchtend oder ich bin zumindest froh, zu wissen, weshalb diese Dinge schief gegangen sind. Es war auch 'beruhigend' zu hören, dass die Firma seit 10 Jahren nicht mehr solche Lieferprobleme gehabt habe wie diesen Herbst. Aber es wäre schön gewesen, dies während der Lieferprobleme zu wissen. Aufgeklärt und informiert zu werden. Und es wäre doch einfacher gewesen, wenn mich Herr Stüssi vor der Anhängerlieferung gewarnt oder darüber aufgeklärt hätte, dass z.B. 12 Löcher im Chassis sind, die fälschlicherweise gebohrt wurden, und dass er dies bedaure. Das Bedauern im Nachhinein zu hören, wenn man erst selbst darauf aufmerksam machen musste, hinterlässt schlicht nicht den besten Eindruck.
Bautag 2
Am zweiten Bautag ging es vor allem darum, den Anhänger fertig mit Dämmung 'aufzufüllen'. Wie auf dem ersten Foto ersichtlich, mussten wir zwei Schichten Glaswolle verlegen: Die untere war 6cm dick und quer zum Anänger; die obere war 4cm dick und längs zum Anhänger. Das Schneiden der Glaswolle ging weiter wie am ersten Tag: Mit der normalen Haushaltsschere. Während mein Helfer und meine Helferin die Dämmung zuschnitten und dabei eine super Routine entwickelten, klebte ich auf dem Anhänger noch die restlichen Metallstreben mit Schaumstoff-Randstreifen ab. Danach musste ich mir überlegen, wie viele OSB-Platten ich auf welche Weise auf dem Anhänger anordnen wollte, sodass es möglichst wenig Abfallmaterial und möglichst wenig Arbeit gibt. Dabei kam mir mein Computer sehr gelegen: In meinem Modell baute ich ein paar OSB-Platten und ordnete diese auf dem viruellen Anhänger an. So konnte ich schnell sehen, welche Lösung am besten sein würde.
Daraufhin konnte ich das erste Mal mit einer Handkreissäge hantieren! Ich hatte schon ein wenig Respekt davor. In der Theorie wusste ich bereits, wie das Ding funktioniert, kannte jeden Schalter am Gerät und wusste, wie man die Höhe des Sägeblatts am besten einstellt und worauf man sicherheitstechnisch achten muss. Aber praktisch hatte ich damit noch nie gesägt. Mein erfahrener Kollege, der ab und zu mal ein Möbel selber schreinert, zeigte mir dann vor, wie man es machen muss, und den zweiten Schnitt sägte ich schon selbst. Es ist überhaupt nicht schwer, und trotzdem fühlte ich mich, als wäre ich gerade in die Gilde der Profihandwerker aufgestiegen, haha :D Nein, aber im Ernst, ein super Gefühl, wenn man mit solchen Maschinen umgehen kann. Cool!
Wir schnitten also die erste Platte, welche um den Radkasten gehen sollte, und für diese 'komplexeren' Schnitte kam auch noch die Stichsäge zum Einsatz. Nach dieser Platte war aber Schluss, wir waren alle drei fast verfroren und wollten heim. :-)
Bautag 3
Die Kälte ist wirklich so ein Thema. Bis um 12 Uhr frieren einem die Zehen ein, wenn man bei 0 Grad in einer nicht isolierten Scheune arbeitet; und ab 18 Uhr sinkt die Temperatur wieder drastisch, sodass es einen wieder nach Hause zieht. Ich treibe demnächst einen Heizstrahler auf... Und gehe einfach nicht mehr so früh zum Bauplatz. Die Kälte hat aber noch einen anderen Effekt, den ich total vergessen hatte: Chemische Baustoffe (z.B. Kleber) arbeiten weniger schnell, wenn es so kalt ist! Zum Glück hält der Kleber unter dem Schaumstoff trotzdem; und auch der Silikon, den wir für die Löcher im Anhänger benutzt hatten, war nach zwei Tagen schon trocken...!
Zwischen dem zweiten und dritten Bautag verstrichen einige Tage, in denen ich mir nochmals Gedanken machte über meine Boden-OSB-Platten. Ich hatte ja 15mm-Platten bestellt; auch für die Wände wollte ich 15mm-Platten benutzen. Das Problem war aber, dass wir am zweiten Bautag feststellten, dass sich die 15mm-Platten leicht bogen oder mitwippten, wenn man über sie drüberlief. Besonders in der Mitte des Anhängers, wo die Längsstreben am weitesten auseinander sind. Ich wollte meine Arbeit von Anfang an richtig machen, also entschloss ich mich, jetzt, wo wir erst eine Platte zugeschnitten hatten, nochmals dickere OSB-Platten für den Boden zu bestellen.
Am dritten Bautag fanden wir also die neuen 22mm-OSB-Platten beim Bauplatz vor. Ein kurzer Drüberlauf-Test zeigte: Es war eine gute Entscheidung, diese zu kaufen! Denn nun bewegt sich der Boden überhaupt nicht beim Drübergehen. :-)
Den ganzen Tag verbrachten wir damit, diese 22mm-OSB-Platten passend zuzuschneiden. Wir waren also vor allem am Messen (bereits jetzt nicht meine Lieblingstätigkeit), Einzeichnen und Sägen. Wir massen jeweils zuerst den Anhänger in der Breite aus, um zu wissen, ob er überall genau gleich breit ist (ist er nicht), massen dann die OSB-Platte, um zu testen, ob sie wirklich 2.5 Meter lang war (nie der Fall), und fanden so heraus, was wir abschneiden mussten. Zusätzlich hatte ich beschlossen, die Platten auf beiden kurzen Seiten jeweils 2mm kürzer zu sägen, damit die Enden ein kleines bisschen innerhalb von der Anhängerfläche waren. So verhindere ich, dass die Platte später nicht über den Anhänger rausschaut, denn das wäre hinderlich für andere Bauteile.
Am Abend hatten wir alle ausser der letzten Platte zugeschnitten. Diese wollte ich erst am Schluss zusägen, um auf allfällige Ungenauigkeiten reagieren zu können.
Bautag 4
Gestern war der vierte Bautag: Mein Freund und ich machten uns nun daran, die fertig gesägten Platten am Anhänger anzuschrauben. Dabei fingen wir mit der einen OSB-Platte am Radkasten an. Auf jeder Platte befestigten wir 8 Schrauben, zwei auf jeder Längsstrebe untendran. Details zu den Schrauben: Es waren 5cm lange Blechschrauben mit Senkkopf, 4.8mm breit. Damit diese die OSB-Platten an den Stahlstreben befestigen würden, mussten wir jeweils bei einer Schraube a) das OSB mit einem Holzbohrer vorbohren und b) die Stahlstrebe darunter mit einem Metallbohrer vorbohren.
a) Holzbohrer haben ein charakteristische Spitze, die nie kaputt gehen darf, denn sie ermöglicht erst, dass sich der Bohrer ins Holz bohren kann. Wenn man also mit einem Holzbohrer vorbohrt, wo sich darunter hartes Metall befindet, muss man darauf Acht geben, keinesfalls zu weit vorzubohren - sonst würde die Holzbohrspitze gecrasht werden... Zu diesem Zweck haben wir bei 17mm ein Malerband um den Holzbohrer gewickelt und durch die 22mm-OSB-Platte nie weiter vorgebohrt als bis zum Malerband. Sicherheitsmassnahme!
Info: Wir haben einen 4mm-Holzbohrer benutzt.
b) Mit einem 4mm-Metallbohrer wurde dann der letzte nicht vorgebohrte Teil der OSB-Platte durchstossen und gleich in den Stahlträger gebohrt. Das hat super geklappt. Die Dicke des Bohrers haben wir durch Probieren herausgefunden. Beim 3.5mm-Bohrer hat danach schlicht die Schraube nicht reingepasst, und beim 4mm-Bohrer ging's...
Anschliessend haben wir mit dem Akkuschrauber und dem passenden Bit die Schraube versenkt. Das war manchmal nicht ganz so einfach; teilweise hat der Schrauber nicht so gut gegriffen wie erhofft, teilweise ist die Schraube steckengeblieben... In allen Fällen ausser einem konnten wir die Schraube dann aber mit Gefühl reindrehen.
Das Bohren und Schrauben ging den ganzen Tag. Zum Schluss standen aber noch die letzten beiden Platten an, die noch passend zuzusägen waren. Leider habe ich noch keine Fotos dazu, denn mein Handy und meine Kamera sind wegen der Kälte beide abgestürzt... Nachdem wir diese Platten gesägt hatten, kamen die grössten Schwierigkeiten des Tages. Denn die letzte Platte befindet sich auf offenbar verstärkten Stahlstreben; jedenfalls ging das Reinschrauben überhaupt nicht mehr easy wie vorher. Stattdessen mussten wir die Schrauben mit brachialer Gewalt reindrehen. Bei einer Schraube half gar nichts mehr. Sie steckte einfach fest und wir konnten sie weder rein-, noch rausdrehen. Nicht mal mit der Zange oder mit Handschraubenziehern. Unglaublich, aber die Schraube hat sich so verhakt, dass etwas sehr Erstaunliches passierte: Das Schrauberbit brach bei einem Versuch in zwei Teile!! Es war zwar schon alt und auch etwas angerostet, aber das sollte trotzdem nicht passieren... Naja, jetzt gibt's dann ein Neues... Jedenfalls konnte und kann ich mir nicht erklären, weshalb diese Schraube so feststeckte. Wir probierten noch so lange an der Schraube rum, bis ich ihr den Kopf abriss... Haha ;-) Ups. Jedenfalls schaut jetzt immer noch ein kleiner Teil Schraube raus, den ich unbedingt markieren muss, damit niemand auf die Nase fliegt, bis ich die kaputte Schraube abgefräst habe.
Die Platte hält immerhin! :-)
Jetzt, wo der Subfloor fertig ist, folgt ein aufregender Bauschritt: Die Wände!
Das Holz für die Wände ist bereits vor Ort und fertig zugeschnitten (ich hab es zugeschnitten bestellt). Ab nächster Woche werde ich also damit beschäftigt sein, die Wände zusammenzuschrauben... Juhu!
Kommentar schreiben
René (Dienstag, 21 April 2020 18:20)
So ein cooles Projekt.
Ich habe ein viel einfacheres Projekt vor, ein Vorbau auf Rädern fürs Wintercamping. Also ohne Küche, Toilette oder Schlafmöglichkeit- das haben wir alles im Wohnwagen.
Einen gebrauchten Hänger habe ich bereits gekauft, ein Doppelachser, dieser wird jetzt soweit umgebaut, das ein Plattform entsteht, welche ca. 4.2 x 2.3m gross oder eben klein ist. Beim Boden frage ich mich allerdings, wie die Dämmung (Glaswolle) unten überhaupt hält. Ist die nur einfach reingelegt, fällt die so nicht raus?
Fiona (Mittwoch, 22 April 2020 10:03)
Hallo René :-)
Vielen Dank! Das klingt ja toll, wünsche dir viel Erfolg für dein Projekt!
Mein Anhänger wurde massgefertigt und extra mit geschlossenem Boden konzipiert, das siehst du hier: https://www.tiny-house-projekt.ch/2016/11/25/der-erste-tiny-house-bau-tag-d/
Also es sind von unten abgedichtete Metallplatten am Anhänger befestigt, die diese 'Abteile' im Anhängerboden abschliessen. So konnte ich die Dämmung einfach reinlegen.
Wenn ein Anhänger unten noch offen ist, kann man mit einer Alu-Rolle selber ans Werk gehen und den Anhänger von unten verschliessen, um von oben die Dämmung reinzulegen. Oder man baut einen Unterboden drauf (eine Art liegendes Holzständerwerk), der einseitig mit Alu 'verschlossen' ist. So kann man auch da wieder den Unterboden mit Dämmung füllen. Bei der zweiten Lösung verliert man allerdings etwas Höhe, weshalb ich meine Lösung super fand.
Liebe Grüsse,
Fiona